C: The principle of low melting point and wide expansion temperature range should take into account the influence of sintering temperature on product cost and quality in formulation design. On the one hand, the sintering melting point should be reduced and sintered at a lower temperature to reduce the cost of ceramsite. On the other hand, the temperature range of sintering expansion should be wider to facilitate operation, and more importantly, it is conducive to sintering, so as to avoid roasting accidents.
2. Key Points of Formulation Design
The basic composition of the formula is the formula of the expanded ceramsite, which is composed of the following parts. They are a whole, cooperate with each other, have their own functions and have their own effectiveness.
1) Silicon-aluminium component is the strength source of ceramsite and the basic component of ceramsite. Silicon and aluminium components are mainly supplied by solid waste of silica and aluminium. The main material of this component can be fly ash, tailings, mud, sludge, garbage and so on.
2) The gas-generating component can produce gas at high temperature, which forms a certain gas pressure and makes the ceramsite expand. Carbonate, sulfide, iron oxide, carbon and so on are the main raw materials of gasification components. There are dozens of gas-generating raw materials available, which can be used either alone or in combination. In actual production, one kind of gas-generating material is seldom used alone. In the past, many kinds of compound materials are often used. The principle of selection is based on cheap raw materials with abundant local resources.
3) The main function of bonding component is to improve the viscoplasticity of ceramsite raw materials, especially the viscoplasticity of solid waste, so as to make it have better forming effect. When the particle size of solid waste is very fine and the plasticity is good, the binder components can be omitted. The commonly used binders are clay, CMC, sodium silicate and so on.
4) The main function of flux components is to reduce the melting point of silica-alumina solid waste, so that ceramsite can be sintered at a lower temperature. Proper use of flux components can make the range of burning temperature wider, process better controlled, high quality product rate, and reduce the energy consumption of burning, which is conducive to the realization of low-cost operation of ceramsite.
The main raw materials for flux components are some flux oxides. There are more than 10 kinds of flux oxides in common use. When some solid wastes contain enough flux, they can meet the technical requirements, and the flux components can be omitted.
5) Fuel components mainly provide roasting heat energy to make ceramsite material become melt in its combustion and produce gas to expand. They are often both fuels and gasifiers, and are important components of a multi-function.
Ceramsite calcination
Rotary kiln is the main equipment for calcining ceramsite. Rotary kiln is mainly composed of kiln shell, supporting device (tugboat group), kiln head, kiln tail sealing device, transmission device, feed and calcination device.
After pressing or crushing, raw ceramics materials enter the drying kiln. After drying, raw ceramics balls enter the tail of the calcining kiln from the feed chute. With the rotation of the kiln, they gradually move towards the kiln head. They are discharged through the lower end of the kiln head through the pre-tropical zone, expansion zone and cooling zone. When material (fly ash or shale) enters the expansion zone, it softens and partially liquids with appropriate viscosity. At the same time, gas is generated inside the ceramsite, which expands the fuel. After entering the cooling zone, the material surface is cooled into a hard shell with honeycomb-like porous structure and becomes expanded ceramsite.
Contrary to the trajectory of ceramsite raw meal ball, the hot air generated by flame moves from the kiln head to the kiln tail. The burner sprays the flame into the kiln from the kiln head, and forms a high temperature zone in the burning expansion zone. The raw meal ball moved from the kiln tail is burned and expanded, and then preheated into a hot air stream to continue to move towards the kiln tail. The raw meal ball (coal ash ball or shale particle) just entered the kiln is preheated. Such heat flow movement can make the heat energy and ceramsite achieve full heat exchange and improve the utilization rate of waste heat.
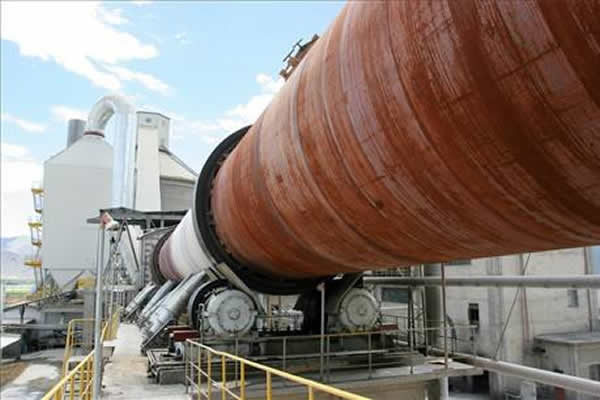
Ceramsite product
Shale, clay, fly ash and other raw materials after calcination in rotary kiln products are finished ceramsite. The main components of ceramsite are mainly SiO 2 and AlO 3. The porosity of ceramsite is very high, generally accounting for 48%~70% of the total volume of ceramsite. It has excellent thermal insulation, lower bulk density and excellent sound absorption and insulation performance.
Composition of ceramisite kiln
Ceramsite rotary kiln is mainly composed of cylinder, kiln tail, supporting device of supporting wheel, transmission device, kiln head, supporting device of supporting wheel and sealing device.
1. In order to facilitate installation and debugging, and to ensure that the main transmission system can be repaired or other abnormal conditions can still be operated in the kiln, to prevent the kiln shell from bending deformation in the cooling process;
2. Rolling bearings are used in supporting devices (and a few of them are sliding bearings), which greatly simplifies the supporting structure of supporting wheels, reduces the useless power loss in the process of kiln operation, and makes maintenance and repair more convenient.
3. The radial contact seal with elastic scales is used for the sealing of kiln tail and kiln head, which can well adapt to the shape error of the cylinder, the yaw and the axial movement of the kiln, and make the sealing performance more excellent.
4. Hydraulic or mechanical retaining wheels are selected according to kiln type. Both of them have high reliability and precision. At the same time, the outer circles of the supporting wheels and wheels wear uniformly in the whole width direction and are easy to adjust.
5. There is a special gap between the tyre and the cylinder to ensure that the tyre tightening hoop plays a role in strengthening the cylinder after the thermal expansion of the cylinder.
6. The big gear ring is a split combined structure, which is connected with the cylinder body by spring plate. It is easy to install, and the transmission is stable and reliable.
7. Two to three fulcrums of the whole kiln can easily ensure that the contact surface between the supporting wheel and the kiln wheel belt is parallel to the axis of the cylinder body when installed.
Specification and technical parameters of ceramsite rotary kiln
Design ability |
25000m³/y |
30000m³/y |
45000m³/y |
60000m³/y |
100000m³/y |
product |
ceramsite |
ceramsite |
ceramsite |
ceramsite |
ceramsite |
cooler |
Cooling form |
Air cooling |
Air cooling |
Air cooling |
Air cooling |
Air cooling |
appearance |
circular |
circular |
circular |
circular |
circular |
Specifications |
0.8x10m |
1.0x10m |
1.2x12m |
1.5x15m |
2.0x20m |
power(kw) |
7.5 |
11 |
15 |
18.5 |
30 |
Rotary kiln |
Specifications |
¢1.6x28m |
¢1.9x30m |
¢2.2x30m |
¢2.5x36m |
¢3.0x48m |
Slope(%) |
3.90 |
3.90 |
3.90 |
3.90 |
3.90 |
speed(r/m) |
1.2-3.5 |
1.2-3.5 |
1.0-3.5 |
1.0-3.5 |
1.0-3.5 |
power(kw) |
22 |
30 |
45 |
75 |
90 |
weight |
38 |
60 |
95 |
110 |
220 |